Akvaplan-niva is building a new research and innovation station on Kvaløya outside Tromsø to replace the existing infrastructure at its Fisk facility, which conducts experimental work with marine species. Photo: Fisk
A new research and innovation station being built by Akvaplan-niva on Kvaløya outside Tromsø will be able to achieve perfect water temperatures courtesy of PTG. That helps in cracking the code when seeking to farm new marine species.
Since its foundation in 1984, Akvaplan-niva has offered environmental consultancy services and research related to aquaculture and the aquatic environment. Its Kraknes station near the north Norwegian city of Tromsø conducts experimental work with marine species, and it holds farming licences for more than 130 of these.
“You’d have to search closely to find a species from northern waters which isn’t on this list,” says Trond Ivarjord, section manager at the Kraknes research and innovation station, better known as Fisk from the acronym for its Norwegian name. Helpfully, this also means “fish”.
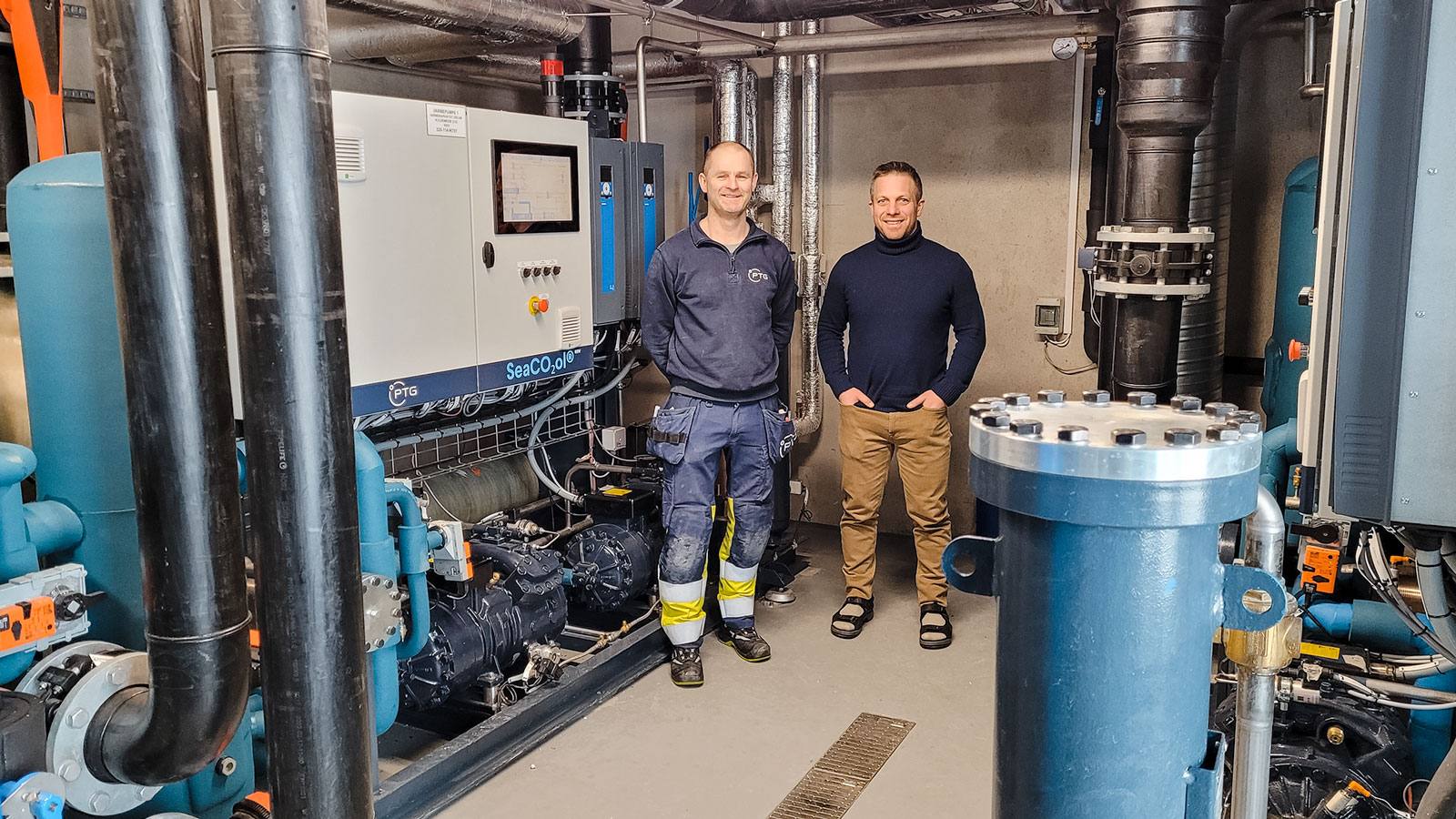
PTG project manager Rune Skogly Olsen (left) and Fisk section head Trond Ivarjord are currently testing the climate plant at the new Kraknes research station. Photo: Fisk
Help to begin
“We work at the interface between research and commercialisation, often with companies in a start-up phase which need support to get the wheels turning,” Ivarjord explains. “We can help them to begin production on a small scale.”
He points to specific projects on farming such species as kelp, cod, lumpfish and spotted wolffish. And stable water temperatures represent an important requirement when researching new candidates for commercial rearing.
They are necessary for ensuring not only that each trial in a series is comparable, but also that the fish being studied will grow and be assured of good welfare conditions.
“Cod and wolffish roe, for example, are very sensitive to excessive temperatures,” says Ivarjord. “If the water’s too warm, larvae and fry could die or become deformed.
“Up here in the far north, seawater has an autumn temperature of 9–10°C . We can’t use that, even if we extract it from a depth of 60 metres. We’re then utterly dependent on being able to cool down the water to 5–6°C and keeping it there.”
Efficient and reliable temperature management is therefore extremely important for Fisk, and this was given great emphasis when designing its new research station.
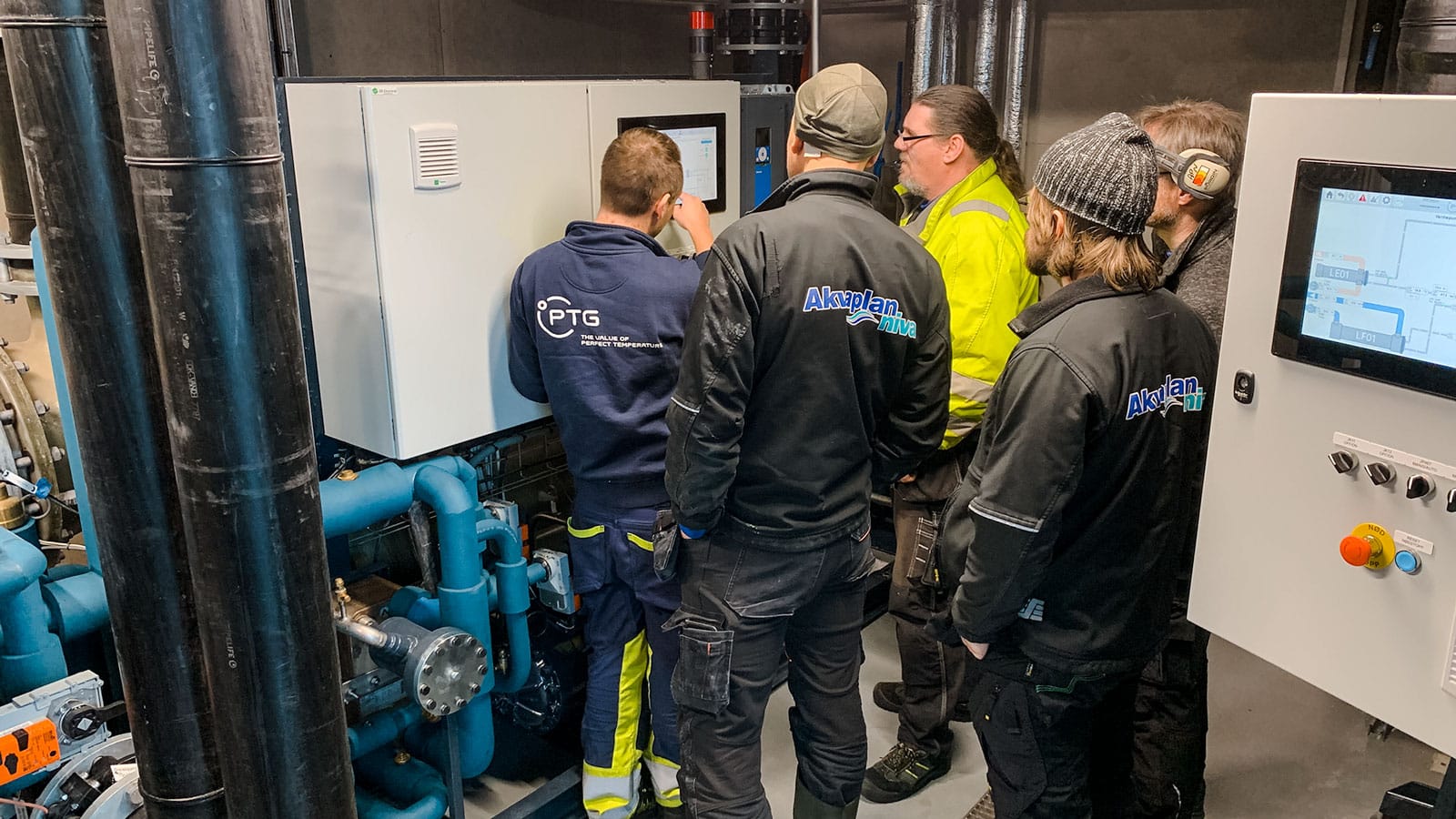
PTG automation engineer Aleksander Norgård (left) training technical personnel from Akvaplan-niva. He has played a key role in the project with regard to programming and setting up automation for the whole plant – including interfacing with the other deliveries. Photo: PTG
Advanced and complex
“The plant we’ve now established is technically advanced and highly complex,” reports Raymond Enoksen. He is a sales engineer and project developer at PTG – Perfect Temperature Group, which has supplied climate technology for the new station.
This forms part of a water treatment and process facility delivered together with Unik Filtersystem – the turnkey contractor for the complete plant – as well as Preplaset, Alde Akva and Eltro.
“Three different water temperatures are to be kept constant throughout the year and under all operating conditions,” explains Enoksen. “That calls for a lot of energy, and 80 per cent of this is recovered by waste heat exchangers – in other words, water pumped into the station swaps heat with both hot and cold waste water.
“An important part of our delivery is two SeaCool CO2 heat pumps working directly against seawater. In other words, the intake water is in direct contact with the evaporator and condenser in the heat pumps.
“That saves both energy and space, since we don’t need to install a secondary circuit. In addition, CO2 is a natural refrigerant without documented negative effects on the environment.”
He adds that, in addition to delivering climate solutions, PTG has been responsible for extensive automation between the various systems in order to ensure that everything works together properly.
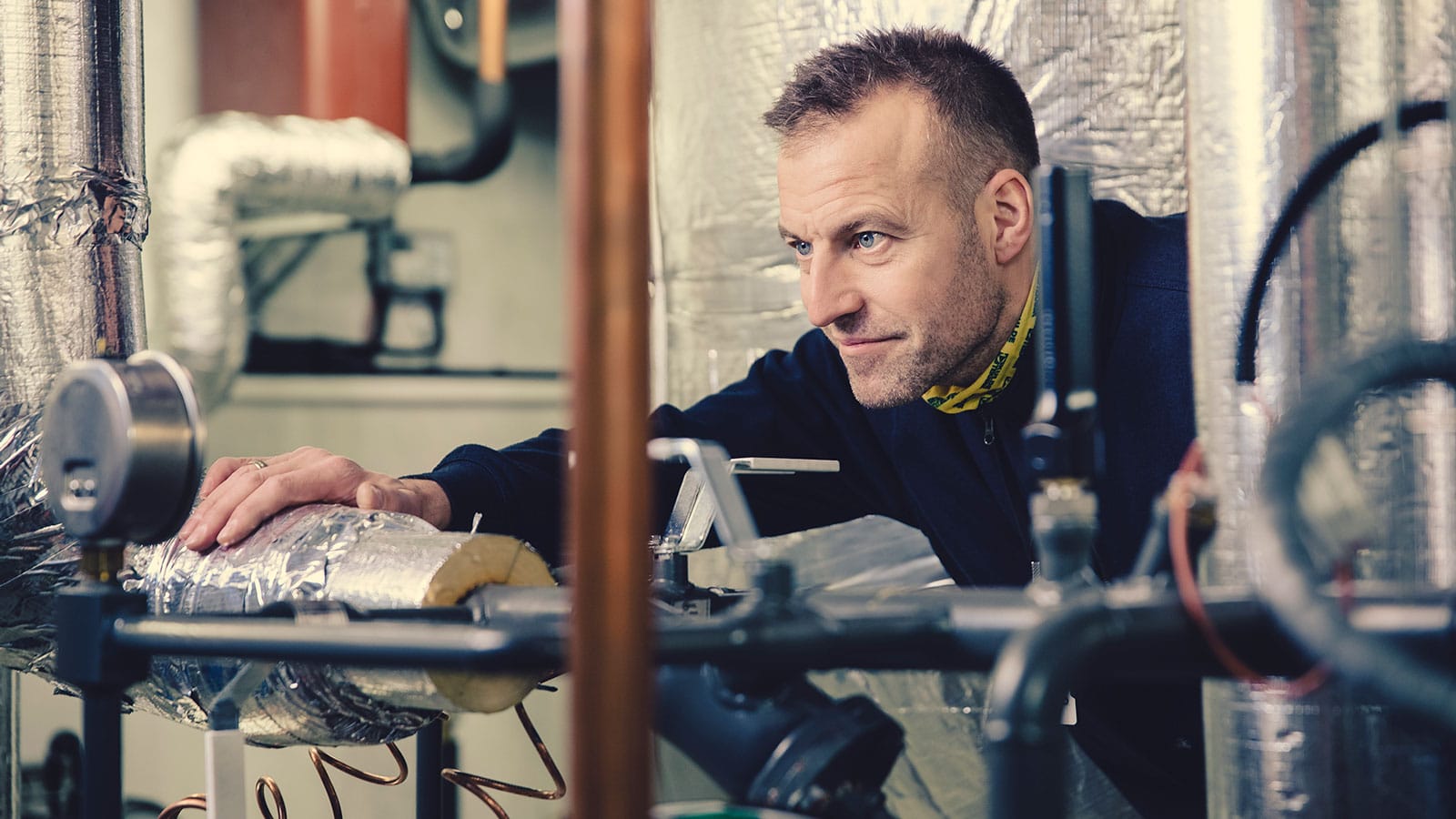
“This is a technically advanced and highly complex plant,” reports Raymond Enoksen, sales engineer and project developer at PTG – Perfect Temperature Group. Photo: Marius Fiskum
Extensive trial operation
Stability in every operating phase is also important. Even though the new plant has just been handed over from the developer to Fisk, extensive trials remain to be run before the process plant is ready for use.
Rune Skogly Olsen, PTG’s project manager, reports that priority is given to the survival and welfare of the fish, with great attention concentrated on stability.
“The fish must be able to survive a possible long-lasting power cut, for example. All circuits therefore have a double set of critical components – known as redundancy – and power supplied by emergency generators prioritises those elements which ensure fish survival.”
Preliminary tests show that the plant can also be run at almost full capacity on emergency power, he adds.
“It’s interesting and exciting to be able to contribute to a plant with the ambitions which Akvaplan-niva has for Fisk. Through our delivery, we’re helping to enable research on Arctic marine species for commercial development of the aquaculture industry.”
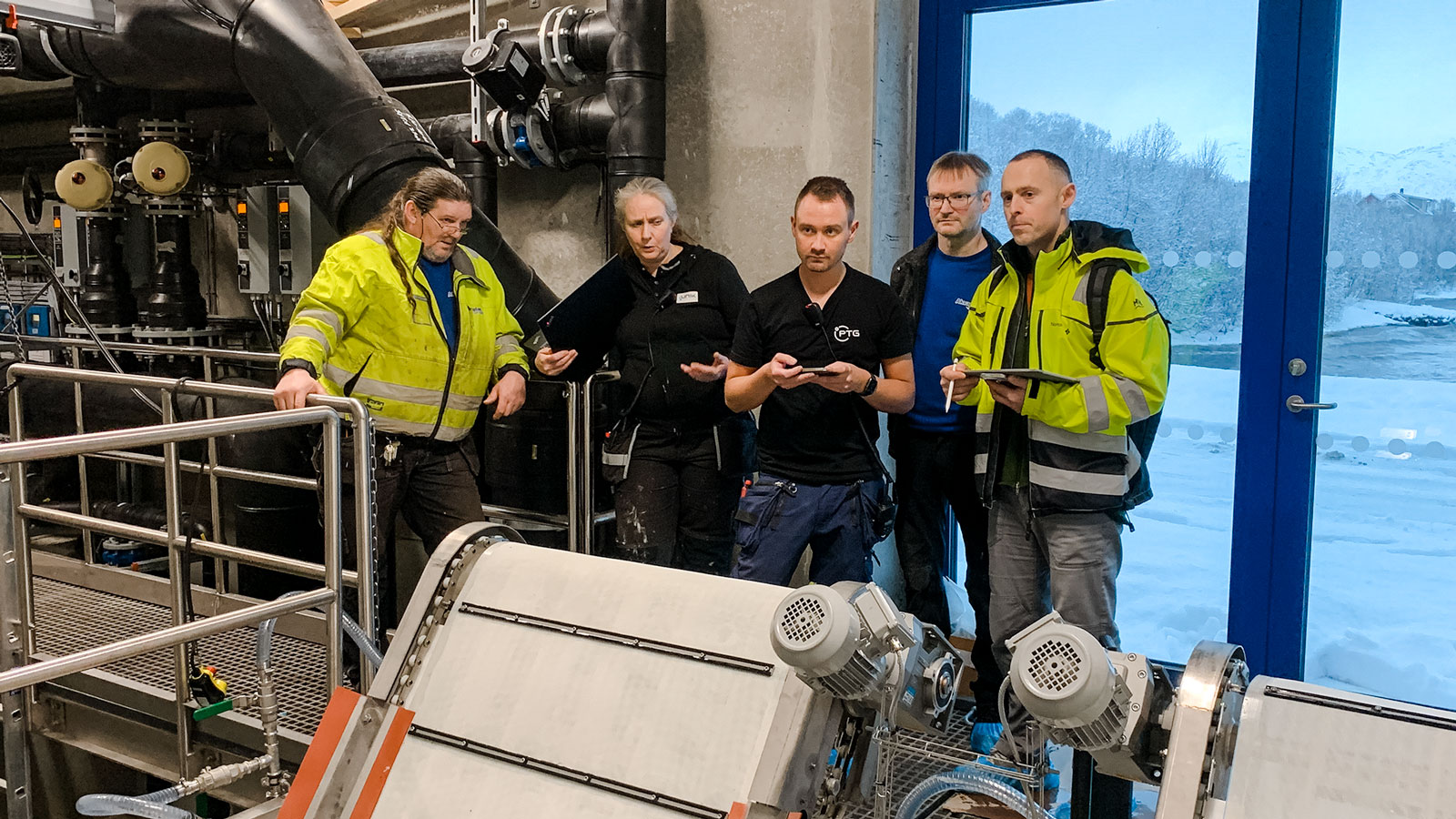
Function-testing the new process plant before it comes into use. From left: William Kristiansen, Akvaplan-niva, Sonja Vika, Unik Filtersystem, Aleksander Norgård, PTG, Anders Eilertsen, Akvaplan-niva, and Robert Andre Olsen, Norconsult. Photo: PTG
Facts about PTG’s delivery to Fisk
PTG’s delivery comprises the following.
- Four 22 kW intake pumps with vacuum system and an overall capacity of 220 litres per second.
- Waste heat exchanger for heated seawater 1500 kW.
- Waste heat exchanger for cooled seawater 385 kW.
- Two SeaCool SC200s with a combined heat output of 496 kW and cooling output of 398 kW. In addition, one RSW/heat pump has an extra 90 kW evaporator for cooling the building and two gas coolers of 120 kW and 30 kW for building heat and tap water respectively.
- Electric boiler of 250 kW for backup heating of seawater.
- Circulation and submersible pumps, plus control, non-return and butterfly valves.
- Ice water, building heat and tap water plant with accumulator tank.
- Quantity, level, temperature and pressure sensors plus energy metering.
- Automation for the whole contract integrated with the industrial control system.
PTG is a sub-contractor to Unik Filtersystem as the main contractor for the project.