PTG Frionordica has delivered industrial heat pumps and refrigerated seawater (RSW) systems since 1983, and ice machines from 1965. Over the past three years, volumes from its Malmefjorden plant have expanded sharply – with a corresponding rise in service and maintenance requirements.
To meet this demand, the company is offering free training in and certification as refrigeration technicians for skilled workers who could contemplate joining its workforce.
One of those keen to welcome new colleagues is service coordinator Vegard Kvamme (23) at Malmefjorden.
Along with workmate, friend and service technician Sondre Mittet (22) from Eidsvåg, he joined PTG at an early age. The pair now want even more people to discover the trade and learn what it has to offer.
“Over a six-year period, I’ve worked in production, procurement and now as service coordinator,” he says. “I see good opportunities to continue developing myself here, and ultimately want to take the opportunity of acquiring more trade certifications.”
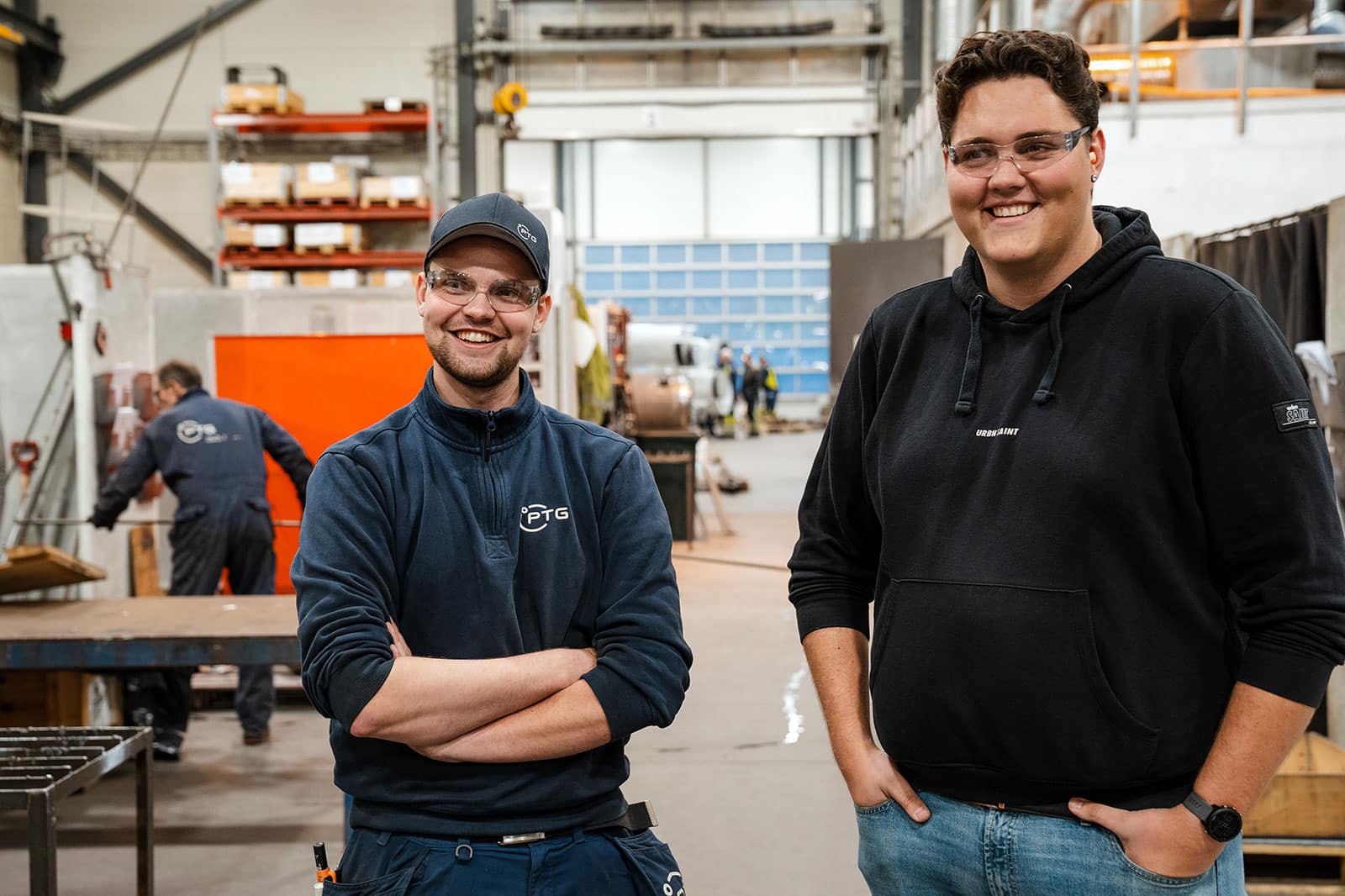
Sondre Mittet (left) and Vegard Kvamme both joined PTG at an early age, and now want more people to become aware of the refrigeration trade and what it has to offer.
Turnover for aftermarket services at PTG Frionordica has doubled over the past year, and this growing workload has also increased the need for more certified service technicians.
Attractive offer
PTG, which ranks as Norway’s leading refrigeration specialist, is now offering free training and trade certification for skilled workers joining its ranks.
“Heating and refrigeration technicians are in very short supply throughout the Nordic region, and far too few are being trained,” says Bjørn Bergseth, service manager for marine and industry at the PTG group. “This qualification is much in demand.”
He reports that the group wants to recruit skilled workers with a technical background, such as mechanics, automation technicians or electricians, and train them to become refrigeration and heating technicians.
Together with local departmental managers like Atle Johansen at Malmefjorden, Bergseth heads PTG’s service teams for the marine and industry sectors.
“We’ll be needing many more employees in coming years,” confirms Johansen. “We see that we’ve got to educate them ourselves to meet market requirements.”
Bergseth adds: “Suitable recruits get a permanent job and receive full pay while qualifying, and we meet the cost of training and certification.”
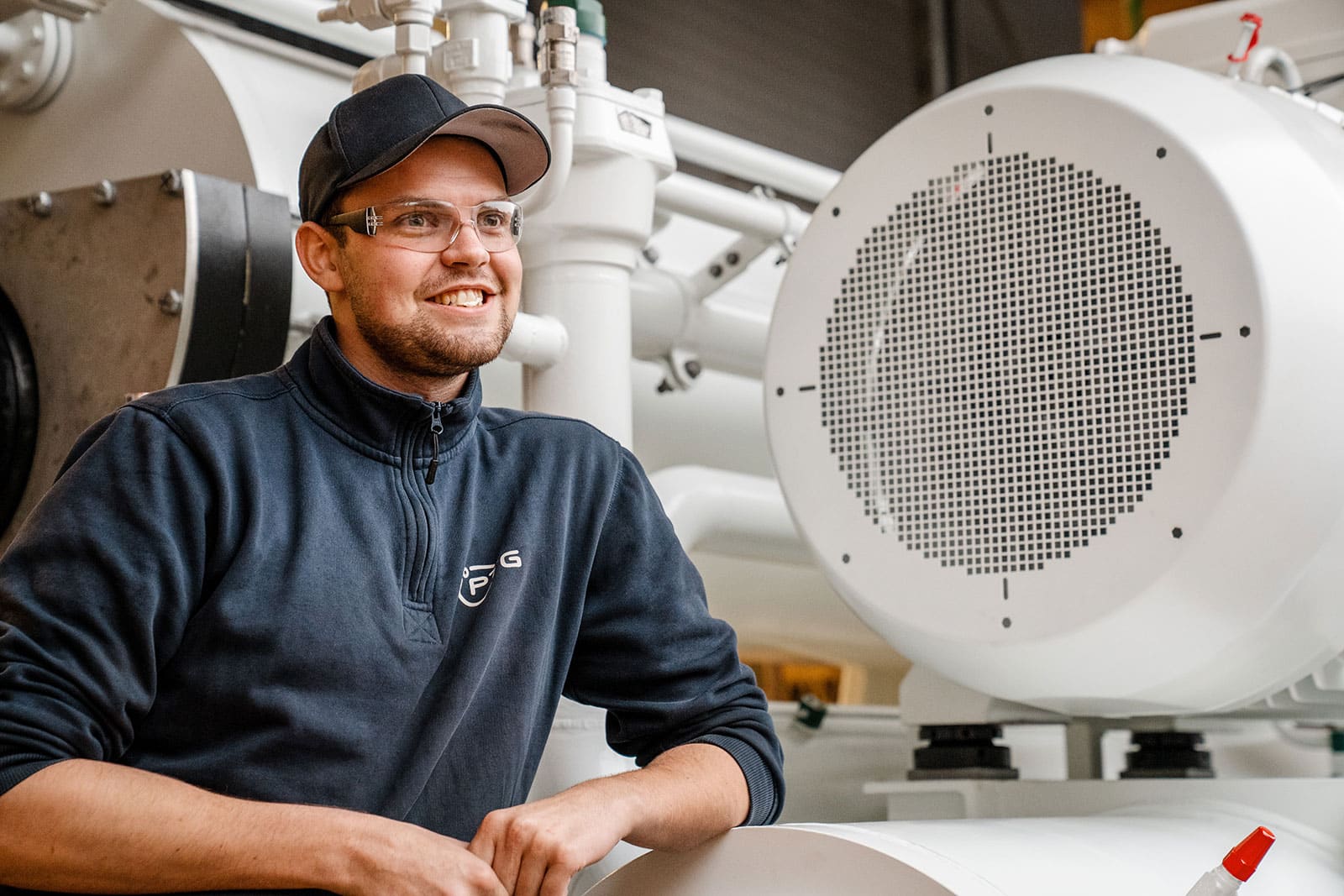
At the age of 22, Sondre Mittet from Eidsvåg is a service technician at PTG Frionordica in Malmefjorden, and learnt about this trade during a school visit while taking the automation course at upper secondary school.
Socially beneficial
“This trade is much bigger than people imagine, and you never stop learning in it,” says Mittet. “You don’t get very far in the modern world without help from somebody with technical expertise in cooling and refrigeration.”
He cites the following example: “That pack of salami you take from the shop fridge cabinet wouldn’t have been there without refrigeration. It certainly wouldn’t have looked very nice. Behind the scenes, cooling is massively important for food production and distribution.”
Kvamme nods in agreement, before adding: “We operate mostly in the first and second stages of the value chain. Fish must be taken from the sea and refrigerated if we’re not to return to salting food in order to preserve it.”
The lads frown and shake their heads. They clearly cannot imagine a better alternative to refrigeration in today’s society.
“Perfect temperature has great social utility and is a very important factor in industry,” Kvamme says. “Take an onshore fish farm, for example. If the temperature isn’t right, the fish don’t grow as they should.
“Aquaculture is important for future food supplies, and not least for improving the energy efficiency of food production and logistical processes.”
He joined PTG as an apprentice six years ago.
“Imagine getting up to a cold sitting room and a warm refrigerator,” he says, and both lads chuckle. “You’d have been calling for a service technician pretty quickly then.”
Big development potential
“The opportunity to develop myself is one of the reasons I’d highlight when asked about why I want to work here,” says Mittet. “PTG has a big network, with many customers and a great deal of expertise in-house.”
Both he and Kvamme agree that being close to the manufacturing process gives them an sense of security and greater expertise as service technicians.
“We have a good mix of people here, from those who’ve been developing products for several decades to brand-new apprentices,” Kvamme observes. “This gives the working day a social dimension, while providing the security of backing from more experienced people.”
Mittet agrees emphatically. “That leads to a lot of friendship, not only with people the same age but also with older colleagues who have lots of experience and expertise to share.”
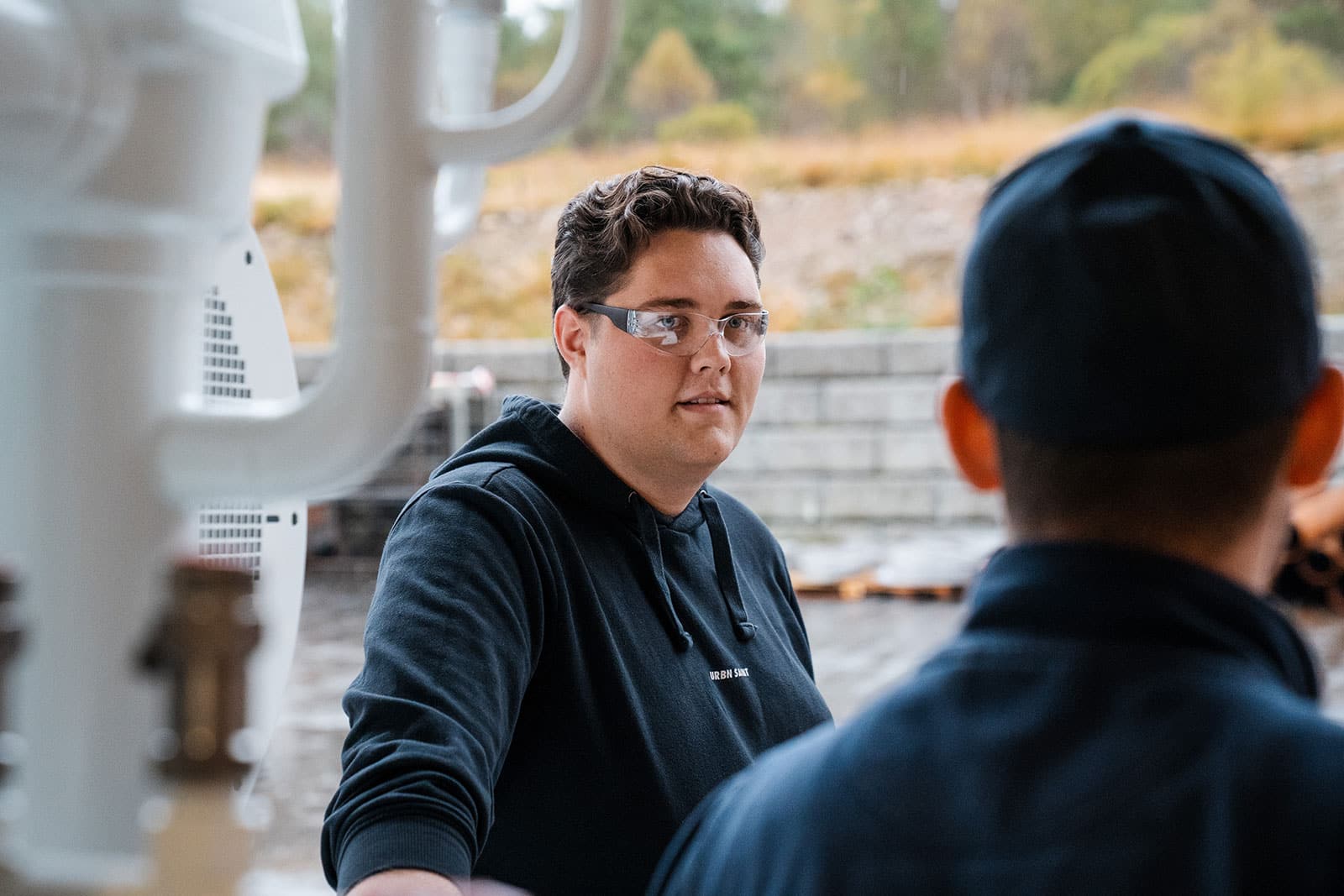
Vegard Kvamme joined PTG as an apprentice more than six years ago. He is now a service coordinator and plans to continue developing himself in the company.
Following the product’s life cycle
A typical working day at PTG can encompass starting up new projects, pursuing planned service assignments and doing acute repairs.
“We visit players large and small across the whole country, and often abroad as well,” reports Johansen. “Our people are out and about starting up new installations at customers in large parts of the world.”
In addition to the big network and good opportunities for further training PTG offered, this interaction between manufacturing and service was one of the major reasons why Kvamme and Mittet joined the group.
“Professionally speaking, there’s a lot to gain from following the product all the way,” says Mittet, who has just returned from a starting up a new plant in Finland. “We wouldn’t have had that chance without all the production taking place in Norway, like here.”
Personnel at PTG are able to follow the process from A to Z, he observes – product development, manufacturing, and assembly, service and repair out at the customers.
“That gives us a unique familiarity with the product and an opportunity to help improve and further develop it.”
Kvamme also appreciates the affiliation employees get to the product and the process.
“You work with innovative products developed in-house, and which make a highly relevant contribution to the goals of reducing energy consumption and pollution,” he says.
Seeking specialists
Uptime is particularly critical for many of PTG’s customers. A number have entered into agreements which ensure that critical components are kept immediately to hand, with quick access to product specialists who can locate and repair possible faults.
“Demand has risen for deals which ensure top-class maintenance, rapid provision of specialist help, service technicians and spare parts, and high priority,” reports Johansen.
“We have service technicians who can mobilise at short notice and systems for virtual support through remote access and fault searching on installations via the internet,” adds Bergseth. “That means we can speedily identify operational errors.”
The result is that customers are looking to product specialists more often.
“Continuously refreshing expertise through courses and certification goes without saying to ensure that all our personnel keep abreast of the latest solutions,” says Johansen.

Bjørn Bergseth (left), service manager for the PTG group, and department manager Atle Johansen at PTG Frionordica report that far too few heating and refrigeration technicians are trained in the Nordic region. PTG has taken action on this by establishing an internal school which offers courses and training.
Meaningful work
While Mittet works out in the field as a service technician, Kvamme has a coordinatory role and serves as the link between technician, customer and supplier.
“I try to ensure that the service technician can do their job as efficiently as possible, with the equipment they need from suppliers and sub-suppliers to do the work in a way which satisfies the client,” he says, and explains that a lot of pieces have to fall into place.
“I feel a nice sense of mastery when the jigsaw’s been completed and we get positive feedback from the customer. When the service technician’s also happy, we can all take a well-earned Friday beer. That improves job satisfaction.”
Mittet also characterises his job as rewarding.
“If it wasn’t, I’d never have stuck with it. Completing a demanding repair job gives you a feeling of being in command, and you can reasonably claim to be proud.”
PTG in brief
PTG develops and delivers environment-friendly cooling, freezing and energy-efficiency solutions. In addition to the seafood market nationally and internationally, the group is a substantial supplier to the retail sector in Norway.
As the leading Norwegian centre of expertise for refrigeration technology, it offers complete solutions for temperature management to the international market, including cooling, freezing, air conditioning and heating.
Production in Norway and an extensive service network allow PTG to meet customer requirements for quality and precise delivery. It is present along much of the Norwegian coast as well as in the UK and Chile.
The PTG name derives from the initials of holding company Perfect Temperature Group and the group’s slogan – the value of perfect temperature.
PTG Frionordica
The former FrioNordica company became part of what is now PTG in 2018.
PTG Frionordica had its origins in Finsam (1965) and Aquaterm (1983), and ranks as Norway’s leading supplier of refrigeration facilities for maritime use. It develops and produces RSW plants and heat pumps for the aquaculture and fishing industries in Norway, Europe and South America.
Until the integration with PTG, its head office was at Malmefjorden near Molde, with a branch in Grimstad and a subsidiary in Chile.
Aftermarket services
Follow-up, such as service and maintenance, once a product has been delivered.
Industrial heat pumps
PTG Frionordica develops, designs and delivers complete FrioNordica heat pump installations for heating and refrigeration applications in aquaculture, such as cooling broodstock and live roe, warming smolt, and refrigeration during harvesting.
FrioNordica heat pumps utilise ammonia (NH3), the most environment-friendly coolant available for low-temperature heat pumps.
PTG also develops and delivers heat pumps with CO2 as the coolant.
RSW plants
RSW stands for refrigerated seawater. PTG Frionordica has delivered Frionordica and RSW systems to the international fishing fleet, the coastal fleet, wellboats, land-based fish farms and the fish-processing industry.
FrioNordica RSW systems also make considerable use of NH3 as a natural coolant, which is ideal for these facilities as well as for large industrial installations. SeaCO2ol RSW systems using CO2 as coolant can be offered with PTG’s smaller facilities.
Collectively, PTG’s FrioNordica and SeaCO2ol RSW systems represent a complete range of such solutions based on natural NH3 and CO2 coolants.